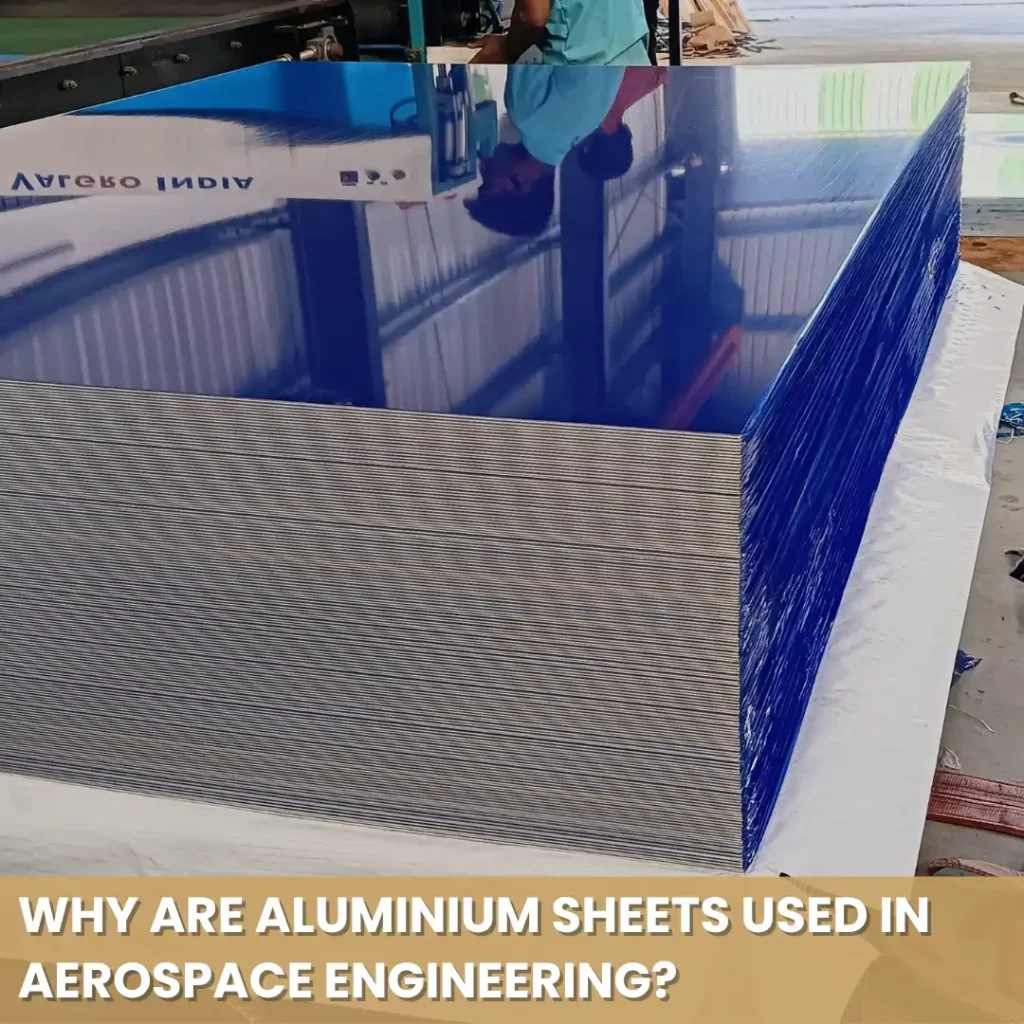
The aerospace industry stands at the forefront of engineering innovation, constantly striving for lighter, stronger, and more efficient materials. Among these, aluminium sheets have emerged as indispensable components. Their unique properties and adaptability have made them a cornerstone in the design and manufacture of aircraft and spacecraft. Here’s a deeper dive into why aluminium sheets are so vital in aerospace engineering:
1. Exceptional Strength-to-Weight Ratio
Aircraft demand materials that can withstand immense stress while keeping weight to a minimum. Aluminium sheets strike this balance perfectly:
- Lightweight Nature: Aluminium is significantly lighter than steel, reducing the overall weight of aircraft and enabling higher fuel efficiency and larger payloads.
- High Strength: Modern aerospace-grade aluminium alloys, like the 7075 and 6061 series, combine lightweight properties with impressive tensile strength, allowing them to endure the physical demands of high-speed flight and turbulence.
2. Corrosion Resistance in Harsh Environments
Aircraft face constant exposure to environments that promote corrosion, such as salty air over oceans, high humidity, and chemical exposure from de-icing agents. Aluminium sheets:
- Naturally form a protective oxide layer, preventing rust and extending the lifespan of components.
- When further treated (e.g., anodizing), their corrosion resistance can be enhanced, making them suitable for both exterior structures like fuselage panels and internal components
3. High Fatigue Resistance for Longevity
In aerospace, materials are subjected to cyclic loading, such as pressurization and depressurization during flight. Fatigue failure is a critical concern:
- Aluminium alloys used in aerospace engineering are designed to withstand repeated cycles without cracking, ensuring safety over the aircraft’s operational life.
- This property is particularly valuable for high-stress areas such as wing skins and landing gear bays.
4. Thermal Conductivity for Heat Management
Managing heat efficiently is critical in aerospace engineering:
- Aluminium’s excellent thermal conductivity helps dissipate heat in engine components, heat shields, and radiators, ensuring optimal performance.
- This thermal management capability reduces the risk of overheating, which is crucial for engine reliability during long flights.
5. Ease of Fabrication and Design Flexibility
Aluminium sheets are prized for their malleability and versatility in manufacturing:
- They can be shaped into complex aerodynamically efficient designs, such as fuselages, wings, and control surfaces.
- Aluminium sheets are also easily joined with other materials using techniques like riveting, welding, or adhesive bonding, streamlining the assembly of intricate aircraft structures.
6. Fuel Efficiency and Environmental Benefits
Weight reduction is directly tied to fuel efficiency in aviation:
- Aluminium’s lightweight properties reduce fuel consumption, cutting operational costs and lowering greenhouse gas emissions.
- Additionally, aluminium is highly recyclable, contributing to the industry’s push towards sustainable practices. Recycling aluminium saves up to 95% of the energy needed to produce new material, aligning with global environmental goals.
Applications of Aluminium Sheets in Aerospace
The versatility of aluminium sheets allows them to serve a wide array of applications in aircraft:
- Fuselage Panels: The aircraft body relies on aluminium sheets for lightweight, durable construction that supports pressurization and aerodynamics.
- Wing Skins: Aluminium sheets provide strength and flexibility to withstand flight dynamics while maintaining minimal weight.
- Interior Components: Used in flooring, walls, and overhead storage bins due to their lightweight and corrosion-resistant nature.
- Thermal Components: Found in radiators, heat shields, and exhaust systems to manage heat effectively.
Future Innovations in Aluminium for Aerospace
As aerospace engineering evolves, so do the applications of aluminium:
- Advanced aluminium-lithium alloys are gaining traction, offering even lighter weights and improved strength.
- Hybrid materials that combine aluminium with composites are being developed for better performance in specific applications.
- Improved fabrication techniques, such as 3D printing with aluminium powders, are revolutionizing component design and reducing production times.
Conclusion
The reliance on aluminium sheets in aerospace engineering stems from their unique combination of lightweight properties, durability, corrosion resistance, and adaptability. These attributes not only meet the rigorous demands of modern aviation but also contribute to sustainability and cost-efficiency. As technology advances, aluminium will continue to play a crucial role in pushing the boundaries of aerospace innovation.